EVOLUTION OF SEARCH SYSTEMS
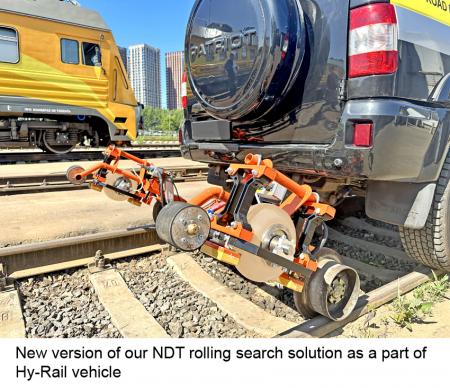
Development of Wheel-Type Search Systems for Rail Flaw Detection
JSC "Firma TVEMA" has consistently demonstrated its commitment to advancing diagnostic systems for railway infrastructure. Among its many innovations, the company has placed significant emphasis on improving non-destructive testing (NDT) systems for rail inspection. Over the years, these efforts have led to groundbreaking developments in ultrasonic flaw detection, ensuring safer and more reliable railway operations worldwide.
Evolution of Rail Inspection Systems: Key Milestones
The journey of innovation in rail flaw detection has been marked by several key milestones, each representing a leap forward in technology and performance:
1. Transition to Friction-Rolling Systems (Early 2000s):
• The shift from friction-sliding systems to friction-rolling systems marked a turning point in rail inspection. This innovation reduced mechanical wear and improved the stability of acoustic contact, laying the foundation for more reliable inspections.
2. Introduction of Contactless Magnetic Centering Systems (2010):
• The adoption of magnetic centering systems eliminated the need for physical contact with the rail, significantly reducing wear and improving alignment accuracy. This breakthrough allowed for more consistent and precise ultrasonic testing.
3. Launch of the ECHO-COMPLEX Series (2012–Present):
• The introduction of the "ECHO-COMPLEX" series of flaw detectors represented a major advancement in hardware capabilities. Each iteration—from "ECHO-COMPLEX" to "ECHO-COMPLEX-4"—expanded the dynamic range and sensitivity of ultrasonic channels, enabling the detection of increasingly subtle flaws.
4. Development of Rolling Search Units (2017):
• In 2017, JSC "Firma TVEMA" began developing rolling search units that utilize elastic materials to improve acoustic contact stability. This innovation was particularly effective in addressing planar changes in the rail surface, such as vertical steps at bolted joints.
5. Advancements in INTEGRAL Software (Ongoing):
• The INTEGRAL software suite has undergone continuous improvements, with the integration of automated flaw analysis being a standout milestone. This shift towards automation has reduced reliance on manual interpretation, increasing both the speed and accuracy of defect identification.
Innovations in Search Systems: Rolling vs. Sliding
One of the most notable areas of innovation has been the development of rolling search units. These systems utilize elastic materials to improve the stability of acoustic contact, particularly when the rail profile changes in plan (e.g., at vertical steps in bolted joints). However, this design introduces challenges in maintaining the directivity of the acoustic field when the rail surface changes in profile, such as on curved tracks or sections with lateral wear. In such cases, periodic adjustments to the angle of inclination are required, which can complicate operations.
In contrast, sliding search systems excel in maintaining stable acoustic contact when the rail surface changes in profile. Their design eliminates the need for frequent adjustments, making them more adaptable to varying track conditions. However, they may struggle with planar changes in the rail surface, where rolling systems perform better.
The Path Forward: Hybrid Solutions and Beyond
Recognizing the strengths and limitations of both rolling and sliding systems, the future of rail flaw detection lies in hybrid solutions that combine the best features of each. By integrating the stability of rolling systems on planar changes with the adaptability of sliding systems on profile changes, these hybrid systems could offer unparalleled performance across diverse track conditions.
Additionally, advancements in material science could lead to the development of more resilient elastic materials for rolling systems, reducing the need for adjustments and improving overall efficiency. The integration of real-time automated adjustments and artificial intelligence (AI) into the INTEGRAL software could further enhance the precision and reliability of flaw detection, paving the way for fully autonomous inspection systems.
JSC "Firma TVEMA" continues to lead the charge in revolutionizing rail inspection technologies. Through relentless innovation in both hardware and software, the company is addressing the complex challenges of modern railway systems. By embracing hybrid solutions, advanced materials, and intelligent automation, the future of non-destructive testing promises to be more accurate, efficient, and reliable than ever before. As the railways of the world evolve, so too will the technologies that keep them safe and operational, with JSC "Firma TVEMA" at the forefront of this transformative journey.